[youtube http://www.youtube.com/watch?v=IbWOQWw1wkM]
Cherry Trunk in the 2012 Mercedes CLS Shooting Brake
The use of wood in automobiles have evolved from structural in the early years to decorative. Now its use is standard in most cars to help soften the feel of the cars interior. Recently the Rolls Royce announced its 2012 Phantom Drophead Coupé would feature teak panelling in its trunk as well as its soft-top cover; inspired by classic racing yachts. This week, Mercedes Benz released their 2012 CLS Shooting Brake with a wooden trunk deck made of American cherry with inlaid smoked oak and aluminum rails.
In case the owner would like to protect the wooden deck, there is an available non-slip mat.
Of course the rest of the interior still has the regular luxury wooden trimmings.
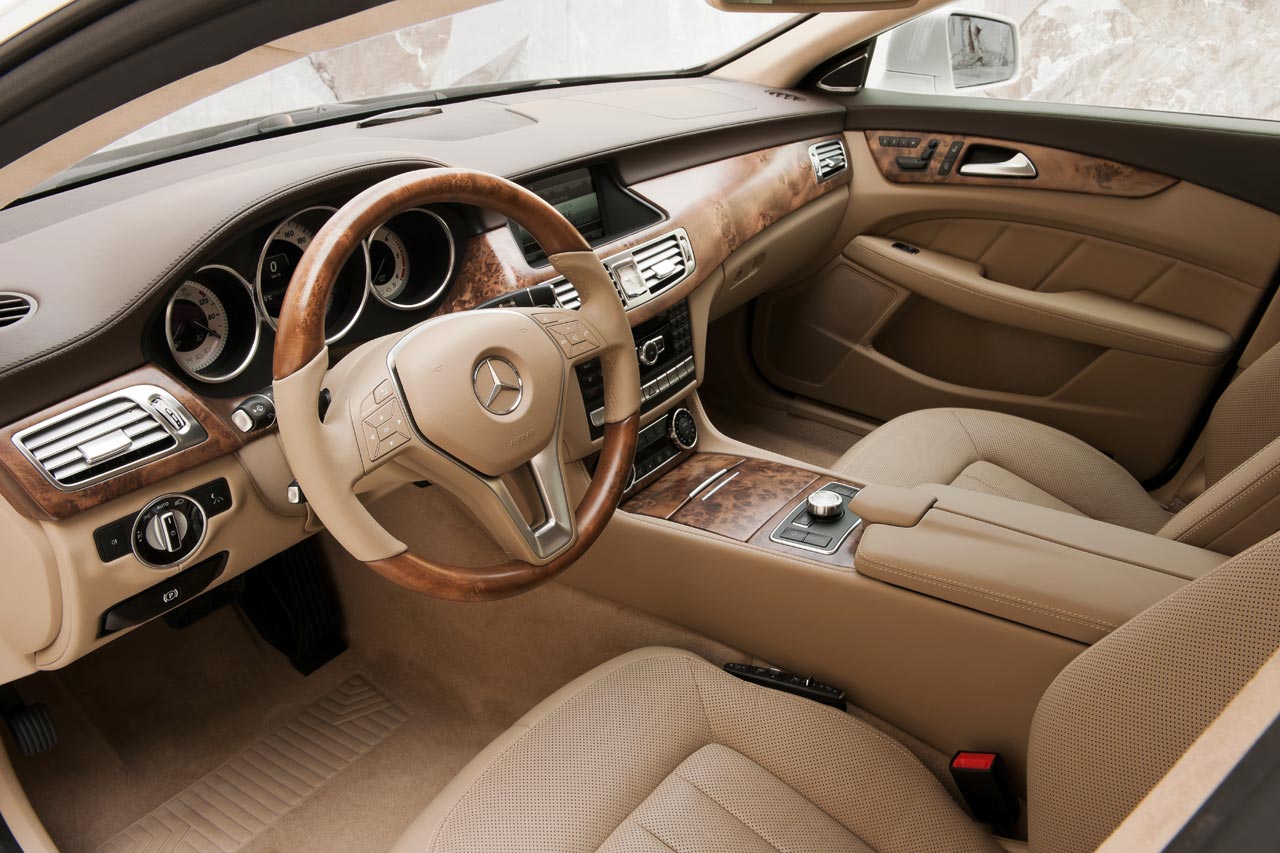
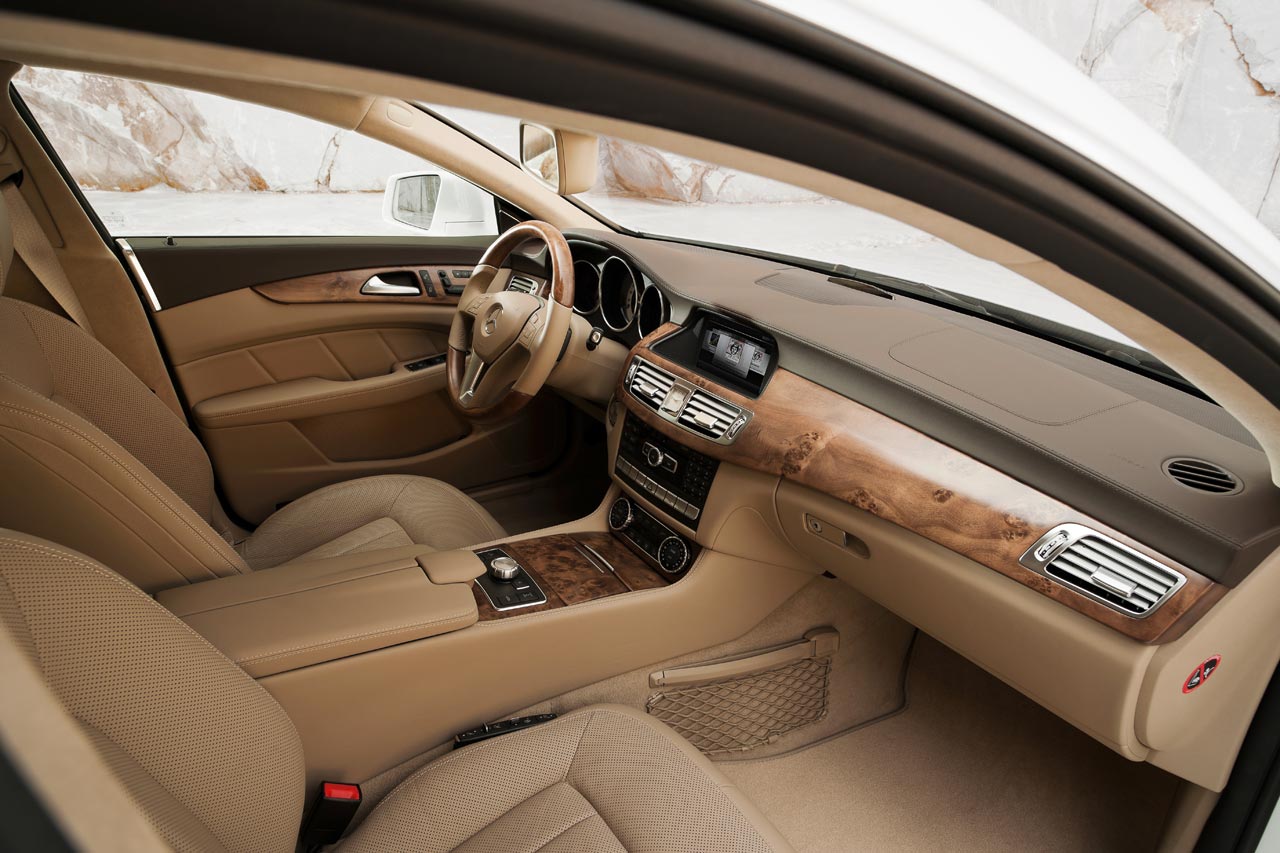
Lexus' Shimamoku Steering Wheel
[youtube=http://youtu.be/mabO5t5alK0]
Louis Vuitton - Trunks
After my History of Industrial Design class last week where we had briefly talked about the early history of Louis Vuitton, I decided that I would check out LV"s flagship store on Fifth Avenue and 57th Street to see if there were any artifacts that might be of interest.
and much to my surprise, there were indeed some vintage trunks on display and unfortunately just out of reach for my little iPhone camera. Here are some grainy photos.
They did have some newer trunks on display.
Here are some images closeup. Notice the variety of materials used inside and out. The chrome hardware does not seem out of place and the wooden trims serve as bumper rails to protect the outer leather surface.
The associate I spoke with at the store gently reminded me that photos are not allowed in store but not before he explained to me that these trunks are much more meaningful when made-to-order especially the cost between one they have in store and a BTO is not as significant as the price tag of one: expensive.
Upon further research it seems Louis Vuitton greatly embraces its proud tradition of luggage for travel. Its website begins with a location imagery that reminds the user of travel.
and is followed by multimedia-rich content that isn't all about commerce but rather presents the company and its heritage in a very pleasing way.
Louis Vuitton also released "100 Legendary Trunks": a book with an accompanying iPad "Interactive Book" app that shows off some of the trunks it has made over the years. Very much worth checking out.
[youtube="http://www.youtube.com/watch?v=d5I5ttT-dvw"]
Caption by Louis Vuitton on YouTube.
Seven crafts performed by hands outlined by daylight. They stitch the skin of a Speedy bag with beeswax-coated yarn, hollow a pea jacket at the waist, sheath the trunk case of a Wardrobe with a creaser, smooth a shoe upper to perfection, scour the contours of a Craquantes jewel, coat the arms of a pair of glasses, file the bevels of a Tambour movement.... Gestures speak. Instruments confer. Words are silent. Passion is revealed.
Bruno Aveillan brings his artist's eye to the House's know-how, passing it on in turn, in his own way.
A website for Dimensional Changes in Wood
woodchanges.com is a website that visually represents of the change that occur in wood over a variety of variables. Of course the theory behind it all lays in the fact that wood is a hygroscopic material, such that it exchanges moisture with its surrounding environment (As a piece of wood looses moisture it shrinks and as wood gains moisture back it swells).
Here are a few screen shots of the charts displaying information over 12 months in New York.
Temperature, Humidity and Moisture Content
Wood Absolute Dimensional Change
Wood Relative Dimensional Change
This kind of information is extremely valuable for furniture makers or wood workers who may find their products crossing international boundaries.
Titanium and Steel Bikes by Budnitz
According to Budnitz Bicycles, Paul Budnitz began creating bicycles for his own use in 2006 while running Kidrobot. By 2010 people were stopping him on the street and asked where they could get a bicycle like the one he was riding. Several offered to buy his bike right out from under him! The bikes are classic-looking and built to last. Depending on the model, the bike frames are made of either brushed titanium or gloss black True-Temper™ cro-moly steel (chromium, molybdenum, steel alloy).
In my opinion, the standout bike in their lineup is the No. 3 Honey Edition. According to the company's description, the bike is:
a classic remix of our Model No.3. German-made 2-inch creme tires, a titanium honey leather Brooks saddle and matching leather grips, titanium badges and our gloss-black city-bike frame.
Not only is there a material change, but it is also highlighted by a change in color.
Just looking at the closeup of the Honey Edition, it is not only aesthetically compelling but the honey leather handles and seat gives it a much warmer look. White tires suggest it will get dirty very quickly in city streets (not sure if one would want to abuse this bike by riding it on city streets) perhaps the owner's intent for owning a bike like this would be for leisure, perhaps better served by the beach.
Words, wood pulp, carbon fiber and kevlar.
Cellulose Nanocrystals, also known as "CNC", can be made from wood chips and saw dust. prepared properly, CNCs can be stronger, stiffer and cheaper than Kevlar and carbon fiber and carry similar light-weight characteristics. These qualities have attracted military interest for use in lightweight armor and ballistic glass, as well as automotive, aerospace, electronics, consumer products and medical industries. The US Forest Service, Forest Products Laboratory, has opened a US$1.7 million pilot plant for the production of cellulose nanocrystals.
Cellulose is the most abundant biological polymer on the planet and is found in the cell walls of plant and bacterial cells. Composed of long chains of glucose molecules, cellulose fibers are arranged in an intricate web that provides both structure and support for plant cells. The primary commercial source for cellulose is wood, which is essentially a network of cellulose fibers held together by a matrix of lignin, another natural polymer which is easily degraded and removed.
Cellulose structures in trees from logs to molecules
Wood pulp is produced in a variety of processes, all of which break down and wash away the lignin, leaving behind a suspension of cellulose fibers in water. A typical cellulose wood fiber is only tens of microns wide and about a millimeter long.
Micrographs of cellulose fibers from wood pulp
The cellulose in wood pulp, when dry, has the consistency of fluff or lint - a layer of wood pulp cellulose has mechanical properties reminiscent of a wet paper towel. Not what you might expect to be the source of one of the strongest materials known to Man. After all, paper is made from the cellulose in wood pulp, and doesn't show extraordinary strength or stiffness.
Cellulose fibers and the smaller structures within them - a) fiber from wood pulp; b) microcrystalline cellulose; c) microfibrils of cellulose; d) nanofibrils of cellulose; e) cellulose nanocrystals from wood pulp; f) CNCs from sea squirts (the only animal source of cellulose microfibrils); and g,h) cellulose nanofibrils from other sources
Further processing breaks the cellulose fibers down into nanofibrils, which are about a thousand times smaller than the fibers. In the nanofibrils, cellulose takes the form of three-dimensional stacks of unbranched, long strands of glucose molecules, which are held together by hydrogen bonding. While not being "real" chemical bonds, hydrogen bonds between cellulose molecules are rather strong, adding to the strength and stiffness of cellulose nanocrystals.
The upper figure shows the structure of the cellulose polymer; the middle figure shows a nanofibril containing both crystalline and amorphous cellulose; the lower figure shows the cellulose nanocrystals after the amorphous cellulose is removed by acid hydrolysis
Within these nanofibrils are regions which are very well ordered, in which cellulose chains are closely packed in parallel with one another. Typically, several of these crystalline regions appear along a single nanofibril, and are separated by amorphous regions which do not exhibit a large degree of order. Individual cellulose nanocrystals are then produced by dissolving the amorphous regions using a strong acid.
At present the yield for separating CNCs from wood pulp is about 30 percent. There are prospects for minor improvements, but the limiting factor is the ratio of crystalline to amorphous cellulose in the source material. A near-term goal for the cost of CNCs is $10 per kilogram, but large-scale production should reduce that figure to one or two dollars a kilo.
Cross-sectional structure of various types of cellulose nanocrystals showing various crystalline arrangements of the individual cellulose polymer molecules (the rectangular boxes)
CNCs separated from wood pulp are typically a fraction of a micron long and have a square cross-section a few nanometers on a side. Their bulk density is low at 1.6 g/cc, but they exhibit incredible strength. An elastic modulus of nearly 150 GPa, and a tensile strength of nearly 10 GPa.
Material | Elastic Modulus (GPa) | Tensile Strength (GPa) |
Cellulose Nanocrystals | 150 | 7.5 |
Kevlar 49 | 125 | 3.5 |
Carbon fiber | 150 | 3.5 |
Carbon nanotubes | 300 | 20 |
Stainless steel | 200 | 0.5 |
Oak | 10 | 0.1 |
The only reinforcing material that is stronger than cellulose nanocrystals is a carbon nanotube, which costs about 100 times as much. Stainless steel is included solely as a comparison to conventional materials. The relatively very low strength and modulus of oak points out how much the structure of a composite material can degrade the mechanical properties of reinforcing materials.
As with most things, cellulose nanocrystals are not a perfect material. Their greatest nemesis is water. Cellulose is not soluble in water, nor does it depolymerize. The ether bonds between the glucose units of the cellulose molecule are not easily broken apart, requiring strong acids to enable cleavage reactions.
The hydrogen bonds between the cellulose molecules are also too strong in aggregate to be broken by encroaching water molecules. Indeed, crystalline cellulose requires treatment by water at 320° C and 250 atmospheres of pressure before enough water intercalates between the cellulose molecules to cause them to become amorphous in structure. The cellulose is still not soluble, just disordered from their near-perfect stacking in the crystalline structure.
But cellulose contains hydroxyl (OH) groups which protrude laterally along the cellulose molecule. These can form hydrogen bonds with water molecules, resulting in cellulose being hydrophilic (a drop of water will tend to spread across the cellulose surface). Given enough water, cellulose will become engorged with water, swelling to nearly double its dry volume.
Swelling introduces a large number of nano-defects in the cellulose structure. Although there is little swelling of a single CNC, water can penetrate into amorphous cellulose with ease, pushing apart the individual cellulose molecules in those regions. In addition, the bonds and interfaces between neighboring CNC will be disrupted, thereby significantly reducing the strength of any material reinforced with CNCs. To make matters worse, water can move easily over the surface/interfaces of the CNCs, thereby allowing water to penetrate far into a composite containing CNCs.
There are several approaches to make CNC composite materials viable choices for real world applications. The simplest, but most limited, is to choose applications in which the composite will not be exposed to water. Another is to alter the surface chemistry of the cellulose so that it becomes hydrophobic, or water-repelling. This is easy enough to do, but will likely substantially degrade the mechanical properties of the altered CNCs. A third approach is to choose a matrix material which is hydrophobic, and preferably that forms a hydrophobic interface with CNCs. While not particularly difficult from a purely chemical viewpoint, there is the practical difficulty that interfaces between hydrophobic and hydrophilic materials are usually severely lacking in strength.
Perhaps the most practical approach will simply be to paint or otherwise coat CNC composite materials in some material that keeps water away. For such a prize - inexpensive strong and rigid materials - we can be sure that innovations will follow to make the theoretical practical.
[Gizmag]
The original title of the Gizmag article is "Wood pulp extract stronger than carbon fiber or Kevlar", in my opinion, skews the reader's initial perception of the material, cellulose nanocrystals, at hand, which was most likely the intent of the writer/editor; a common practice for many journalists today. While the shortened title does shed light on part of the process of making the process of the material, it gives the material a perceived quality of being almost miraculous as wood pulp is a common, low cost, easily achieved industrial product. Upon further reading of the article does the reader start to understand that wood pulp is only an intermediate state a production process and that further studies and improvement will yield a practical, inexpensive product.
In this case, I'm learning to not judge the article by the material or materials mentioned in its title.
Gold Plated Nike Zoom Force 1 - Product by Process
After finally taking some time off from work, I'm finally back to attack the final semester of my time at Pratt. Here's an video that serves as a good inspiration for such an occasion Posted on Vimeo regarding the making of "American Eagle". Filmed by Ronin of HotMop Films, he spent 9 days filming Osamu Koyama, an artist who built a gold-plated armor for a blank Nike Zoom Force 1, a commission from Nike for their Shoeshine Project 2012.
AMERICAN EAGLE from Hot Mop Films on Vimeo.